Navigating the Tariff Maze: A Supply Chain Risk Owner’s Roadmap for 2025
The global trade landscape just shifted again! April 2025 saw the implementation of new import tariffs across several key sectors, and if you’re a supply chain risk owner, you’re likely feeling the tremors. These aren’t just minor cost adjustments; they represent a fundamental reshaping of international commerce, demanding a proactive and strategic response. The stakes are high. A recent report by the International Trade Consortium estimates that these new tariffs could increase the cost of goods for some businesses by as much as 15% within the next year. Ignoring this reality is no longer an option; understanding and mitigating the risks while identifying potential opportunities is now paramount for supply chain resilience and growth.
This article dives deep into the implications of these 2025 import tariffs for supply chain risk management. We’ll explore the multifaceted ways these tariffs exert pressure on your operations, and more importantly, we’ll equip you with nine concrete strategies to not only weather the storm but also to potentially capitalise on the changing tides. So, buckle up, because navigating this new tariff terrain requires agility, foresight, and a willingness to adapt. Let’s get started!
What Do New Tariffs Mean for Supply Chain Risk Management in 2025?
The introduction of new import tariffs in 2025 throws a significant wrench into the well-oiled machine of global supply chains. For supply chain risk management, this translates into a heightened level of complexity and a broader spectrum of potential disruptions. It’s no longer just about managing supplier relationships or logistical hurdles; tariffs introduce a layer of financial and strategic uncertainty that permeates every aspect of the supply chain.
Think about it! Suddenly, the cost assumptions you’ve built your models on are no longer valid. The carefully negotiated prices with overseas suppliers might now be subject to significant surcharges, impacting your profit margins and potentially your competitive pricing. This immediate financial impact is just the tip of the iceberg.
These tariffs can trigger a cascade of risks across the entire supply chain ecosystem. They can lead to:
- Increased Costs: This is the most direct and obvious impact. Tariffs act as a tax on imported goods, directly increasing the cost of raw materials, components, and finished products. This can squeeze margins, force price increases for consumers, and potentially reduce demand.
- Supply Chain Disruption: As tariffs make certain import sources less attractive, businesses may need to rapidly shift their sourcing strategies. This can lead to disruptions as new suppliers are onboarded, quality control processes are established, and logistical networks are reconfigured.
- Demand Fluctuations: Increased prices due to tariffs can lead to a decrease in demand for certain goods. Conversely, tariffs on competing products might create unexpected surges in demand for domestically produced alternatives or imports from countries not subject to the tariffs.
- Geopolitical Instability: The imposition of tariffs can be a symptom or a cause of broader geopolitical tensions. This can lead to further trade disputes, retaliatory tariffs, and increased uncertainty in international trade relations, making long-term planning incredibly challenging.
- Compliance Challenges: Navigating the complexities of new tariff regulations, including rules of origin, documentation requirements, and potential exemptions, can be a significant administrative burden and increase the risk of non-compliance penalties.
- Increased Competition: Domestic industries protected by tariffs might become more competitive, putting pressure on businesses that rely on imported goods. Similarly, businesses in countries not subject to the tariffs might gain a competitive advantage in markets affected by them.
Essentially, new import tariffs amplify existing supply chain risks and introduce entirely new ones. Supply chain risk owners in 2025 must adopt a more dynamic and holistic approach to risk management, one that explicitly considers the impact of trade policy on every decision.
12 Reasons Import Tariffs Impact on Supply Chain Risk Management
The impact of import tariffs on supply chain risk management is far-reaching and multifaceted. Here are 12 key reasons why these tariffs demand the attention of every supply chain risk owner:
-
Direct Cost Inflation: This is the most immediate and tangible impact. Tariffs directly increase the price of imported goods, leading to higher costs for manufacturers, distributors, and ultimately consumers. This erodes profit margins and can impact competitiveness. For example, a 10% tariff on imported steel directly increases the cost for automotive manufacturers relying on that material.
-
Increased Price Volatility: Tariffs introduce uncertainty into pricing. Changes in trade policy or the threat of new tariffs can cause significant fluctuations in the cost of imported goods, making budgeting and forecasting more challenging. Imagine trying to set your product prices when the cost of your key components could change drastically overnight due to tariff adjustments.
-
Sourcing Diversification Challenges: When tariffs make traditional import sources less viable, companies are forced to explore alternative suppliers, often in new geographies. This introduces risks related to supplier reliability, quality control, ethical labour practices, and differing regulatory environments. Finding a new supplier of specialised electronics components in a different country, for instance, requires significant due diligence.
-
Logistical Network Disruption: Shifting sourcing patterns necessitates adjustments to logistics networks. New transportation routes, warehousing locations, and customs procedures need to be established, potentially leading to delays, increased transportation costs, and complexities in managing a more dispersed supply chain. Think about the logistical challenges of suddenly needing to ship goods from Southeast Asia instead of China.
-
Working Capital Strain: Higher input costs due to tariffs can significantly increase the working capital requirements of a business. Companies need more funds to finance inventory and accounts payable. This can put a strain on cash flow, especially for smaller and medium-sized enterprises. Holding more inventory at higher tariffed prices ties up significant capital.
-
Demand Forecasting Uncertainty: Tariffs can impact consumer demand in unpredictable ways. Higher prices might lead to decreased demand, while tariffs on competing products could create unexpected surges. Accurate demand forecasting becomes significantly more difficult in this volatile environment. Predicting consumer reaction to price increases on everyday goods due to tariffs is a complex task.
-
Increased Risk of Counterfeit Goods: As tariffs drive up the cost of legitimate imports, the incentive for counterfeit goods to enter the market increases. This poses risks to brand reputation, product safety, and ultimately consumer trust. The risk of counterfeit luxury goods flooding the market increases when tariffs make genuine items more expensive.
-
Compliance and Regulatory Complexity: Navigating the intricacies of tariff regulations, including rules of origin, classification codes, and documentation requirements, can be a significant burden. Errors in compliance can lead to penalties, delays, and even seizure of goods. Understanding the specific HS codes and origin rules for each imported component becomes critical.
-
Geopolitical and Trade Policy Uncertainty: Tariffs are often a tool in broader geopolitical strategies. This means that trade policies can change rapidly and unexpectedly, creating a high degree of uncertainty for businesses engaged in international trade. A sudden escalation in trade tensions between two major economies can have immediate and significant consequences for global supply chains.
-
Erosion of Competitive Advantage: Businesses that rely on cost-effective imports may see their competitive advantage erode as tariffs increase their input costs. This can make it harder to compete with domestic producers or companies sourcing from regions not subject to the tariffs. A company that built its business model on low-cost imported textiles might suddenly find itself at a disadvantage compared to domestic manufacturers.
-
Increased Risk of Supply Chain Bottlenecks: As companies rush to find alternative sourcing or adjust their supply chains, bottlenecks can emerge in transportation, warehousing, and customs processing. These bottlenecks can lead to delays and further increase costs. Ports and customs facilities might become overwhelmed as import patterns shift.
-
Impact on Innovation and Product Development: Higher costs for imported components or materials can stifle innovation and product development. Companies may be forced to use less expensive, lower-quality alternatives or delay the introduction of new products. The ability to incorporate cutting-edge but tariffed technologies into new products might be hampered.
9 Ways Supply Chain Managers Can Avoid/Reduce the Negative Impact of Tariffs and Seize New Business Growth Opportunities from Tariffs
Navigating the complexities of new import tariffs requires a proactive and strategic approach. Here are nine ways supply chain managers can mitigate the negative impacts and potentially uncover new growth opportunities:
-
Thoroughly Analyse Your Current Supply Chain Footprint: The first step is to gain a deep understanding of how the new tariffs will specifically impact your existing supply chain. This involves identifying all imported goods subject to tariffs, quantifying the potential cost increases, and assessing the reliance on specific suppliers and geographies. Conduct a detailed SKU-level analysis to understand the tariff implications for each product. Actionable Step: Create a matrix mapping your key imported materials and components against the new tariff rates and their origin.
-
Explore Sourcing Diversification and Nearshoring/Reshoring: Reducing reliance on tariffed imports is crucial. Actively investigate alternative suppliers in countries not subject to the tariffs. Consider the feasibility of nearshoring (moving production closer to home) or reshoring (bringing production back to your domestic market). Evaluate the total landed cost, including transportation, lead times, and quality control, when considering new sourcing options. Actionable Step: Initiate conversations with potential alternative suppliers in tariff-exempt regions and conduct feasibility studies for nearshoring or reshoring key production processes.
-
Renegotiate Contracts with Existing Suppliers: Engage in open and honest discussions with your current suppliers. Explore options for cost sharing, value engineering, or alternative pricing structures that might help mitigate the impact of tariffs. Long-term partnerships might involve collaborative efforts to find cost efficiencies throughout the supply chain. Actionable Step: Schedule meetings with key suppliers to discuss the tariff implications and explore potential contract adjustments.
-
Optimise Inventory Management Strategies: In a tariff-heavy environment, efficient inventory management becomes even more critical. Carefully balance the need to avoid stockouts with the increased cost of holding inventory due to higher import prices. Explore strategies like postponement, where final product configuration is delayed until demand is clearer, or implementing more agile inventory models. Actionable Step: Review your current inventory levels and forecasting accuracy, and explore opportunities to implement more responsive inventory management techniques.
-
Invest in Supply Chain Technology and Visibility: Enhanced visibility across your supply chain is essential for identifying potential disruptions and reacting quickly to changes. Invest in technologies like advanced analytics, real-time tracking, and supply chain mapping to gain a comprehensive view of your international flows and potential tariff impacts. Actionable Step: Evaluate and implement supply chain visibility platforms that provide real-time data on shipments and potential tariff-related delays.
-
Seek Tariff Relief and Duty Drawback Opportunities: Explore potential avenues for tariff relief, such as applying for exemptions or utilising duty drawback programmes (refunds on duties paid on imported goods that are subsequently exported). Understanding the specific tariff regulations and available relief mechanisms can significantly reduce costs. Actionable Step: Consult with customs brokers and trade compliance experts to identify potential tariff relief or duty drawback opportunities relevant to your imports.
-
Innovate Product Design and Material Usage: Consider redesigning products to reduce reliance on tariffed materials or components. Explore the use of alternative materials that are either domestically sourced or imported from tariff-exempt regions. This can lead to both cost savings and enhanced supply chain resilience. Actionable Step: Engage your R&D and engineering teams to explore product redesign options that minimise the use of tariffed inputs.
-
Explore New Market Opportunities and Export Strategies: While tariffs pose challenges for imports, they can also create new opportunities in domestic markets or in countries where your products might now be more competitive due to tariffs on goods from other nations. Explore new export markets that might be less affected by the tariffs impacting your imports. Actionable Step: Conduct market research to identify potential new domestic or international market opportunities arising from the changed tariff landscape.
-
Foster Collaboration and Communication Across the Organisation: Effectively navigating the tariff landscape requires strong collaboration between procurement, logistics, finance, sales, and legal teams. Open communication and shared understanding of the risks and opportunities are essential for developing and implementing effective mitigation strategies. Actionable Step: Establish a cross-functional task force to address the challenges and opportunities presented by the new import tariffs, ensuring alignment across all relevant departments.
By proactively implementing these strategies, supply chain managers can not only mitigate the negative impacts of the 2025 import tariffs but also position their organisations to seize new business growth opportunities in this evolving global trade environment. The key is to be agile, informed, and ready to adapt to the changing currents of international commerce.
Join Supply Chain Risks group
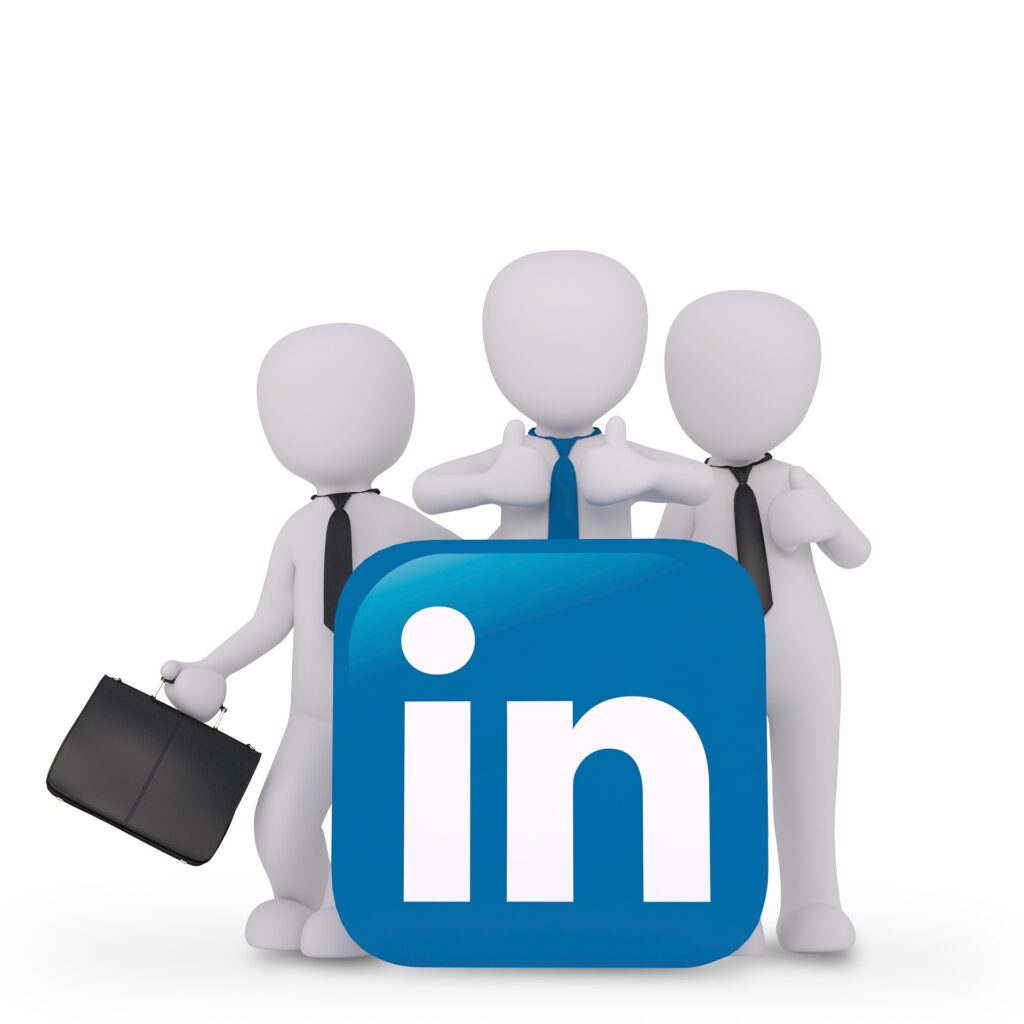
Get help to protect and grow your business faster with less uncertainty with BusinessRiskTV
Find out more about our Business Risk Management Club
Subscribe for free business risk management tips risk reviews and cost reduction ideas
Read more business risk management articles and view videos for free
Read more risk management articles and view videos:
-
How can supply chain risk owners mitigate impact of 2025 import tariffs
-
Best strategies for supply chain managers to avoid negative effects of new tariffs 2025
-
What are the risks of 2025 import tariffs on global supply chain management and how to overcome them
-
Ways to reduce negative impact of 2025 import tariffs and find new growth opportunities in supply chain
-
Actionable strategies for supply chain risk owners to navigate and capitalise on import tariffs in April 2025
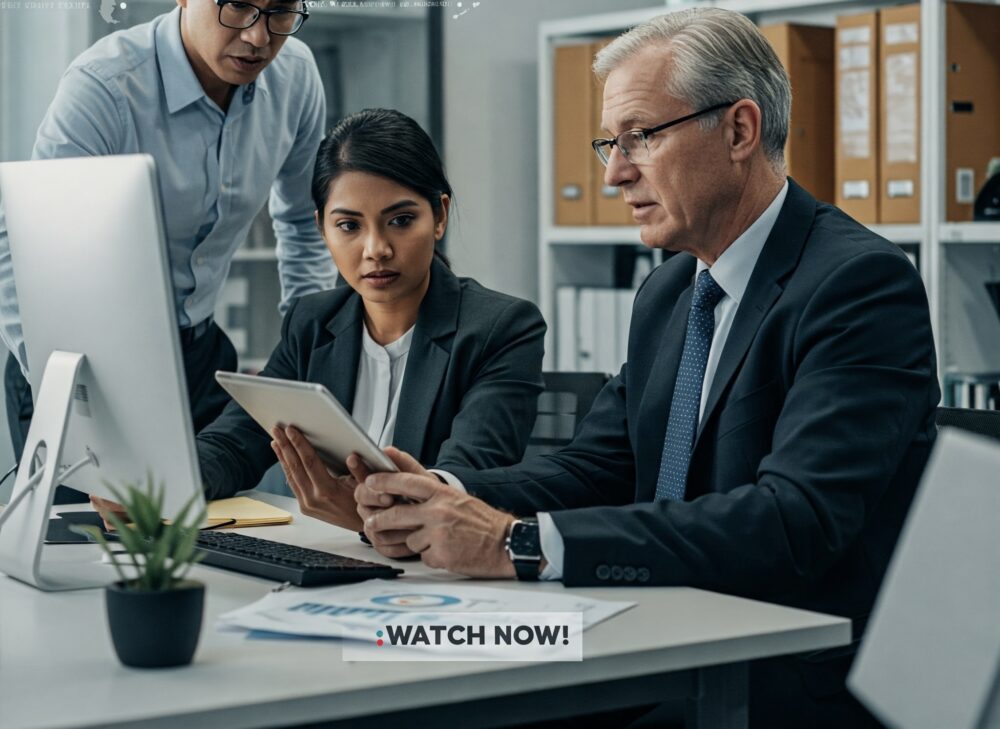
Relevant hashtags:
-
#SupplyChainRisk
-
#ImportTariffs2025
-
#GlobalTrade
-
#SupplyChainManagement
-
#TradeCompliance
Trade Tariffs 2025